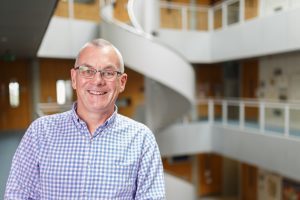
Recognised Expertise in Lean Manufacturing and Employee Engagement.
Noel is the founder and Managing Director of Practical Lean Solutions and has over 25 years’ experience of implementing Continuous Improvement programmes. Noel, in his role as Enterprise Excellence Director at his former employer Lake Region Medical (now Integer) led the site at New Ross, County Wexford to achieve in 2012 the distinction of becoming the first company in any sector in Ireland, and the first medical device company in Europe, to achieve the prestigious Shingo Accreditation. Also in 2012, it was crowned Irish Medical Technology Company of the Year in recognition of its Enterprise Excellence Program.
A committed life-long-learner, Noel’s search for best practices has seen him participate in global benchmarking visits across Europe, Japan, USA, and India; he has an MSc in Lean Operations from Cardiff University; and attained his Doctorate in Business Administration from WIT (now South East Technological University) which focused on the link between involvement in continuous improvement & employee engagement. In 2021, Noel published the Human Lean book with his co-author John Bicheno, which has won both Shingo and Lean Business Ireland Publication Awards.
In October 2023 Noel was inducted into the Shingo Academy Hall of Fame for his contribution to organisational excellence across Ireland and further afield.